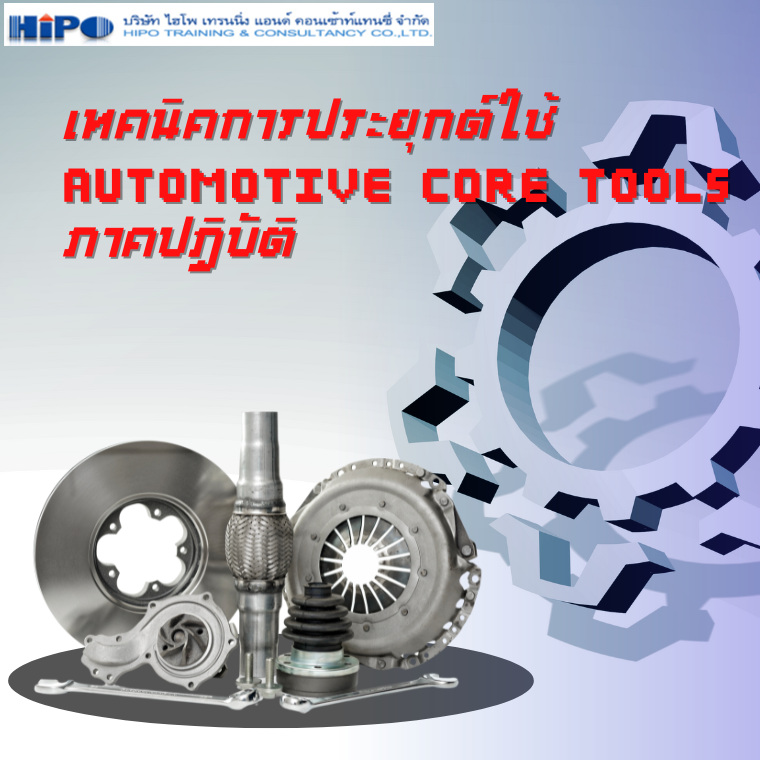
20 กุมภาพันธ์ 2568
ผู้ชม 280 ผู้ชม
สวัสดีครับ! ในโลกของอุตสาหกรรมยานยนต์ที่การแข่งขันสูงลิ่ว และลูกค้าก็คาดหวังคุณภาพระดับสูงสุด "Automotive Core Tools" เปรียบเสมือนอาวุธลับที่จะช่วยให้บริษัทของคุณก้าวไปข้างหน้าได้ แต่... รู้ไหมครับว่าหลายๆ บริษัทยังใช้เครื่องมือเหล่านี้ได้ไม่เต็มศักยภาพ? บทความนี้จะพาคุณไปเจาะลึกเทคนิคการประยุกต์ใช้ Core Tools แบบ "ภาคปฏิบัติ" จริงๆ ไม่ใช่แค่ทฤษฎีในห้องเรียน พร้อมทั้งชี้ให้เห็นปัญหาที่พบบ่อยและวิธีแก้ไข เตรียมตัวให้พร้อมนะครับ เพราะเรากำลังจะยกระดับคุณภาพขององค์กรคุณไปอีกขั้น!
ทำไม Automotive Core Tools ถึงสำคัญ? (หลักการและเหตุผล)
ปัญหาที่พบบ่อยในการนำ IATF 16949:2016 ไปใช้
หลายๆ คนคงเคยเจอปัญหาใช่ไหมครับ? เวลาจะนำมาตรฐาน IATF 16949:2016 มาใช้ในโรงงานจริงๆ มันไม่ง่ายเหมือนอ่านคู่มือ บางทีก็งงกับข้อกำหนด บางทีก็ไม่รู้จะเริ่มต้นตรงไหน หรือทำไปแล้วก็ไม่เห็นผลลัพธ์ที่ชัดเจน นี่แหละครับคือปัญหาคลาสสิก!
Core Tools: กุญแจสำคัญสู่ความสำเร็จ
แล้ว Core Tools มันมาเกี่ยวอะไรด้วย? ก็เพราะว่า Core Tools (APQP, PPAP, FMEA, MSA, SPC) เหล่านี้คือเครื่องมือที่ IATF 16949:2016 กำหนดให้ใช้ไงครับ! พูดง่ายๆ คือ ถ้าอยากจะทำ IATF 16949:2016 ให้ได้ผลจริงๆ ก็ต้องใช้ Core Tools ให้เป็น มันเหมือนกับเรามีเครื่องมือช่างชั้นยอดอยู่ในมือ แต่ถ้าใช้ไม่เป็น...ก็ไม่มีประโยชน์
วัตถุประสงค์และผลที่คาดว่าจะได้รับ (ทำไมต้องเรียนรู้?)
ข้อกำหนด IATF 16949:2016 และ Core Tools
ถ้าเราเข้าใจข้อกำหนดของ IATF 16949:2016 ที่เกี่ยวข้องกับ Core Tools แต่ละตัวอย่างละเอียด เราก็จะรู้ว่า "ทำไม" ต้องทำ และ "ทำอย่างไร" ให้ถูกต้อง ไม่ใช่แค่ทำตามๆ กันไปโดยไม่เข้าใจ
การประยุกต์ใช้เพื่อปรับปรุงคุณภาพ
เป้าหมายสูงสุดของการใช้ Core Tools ก็คือ "การปรับปรุงคุณภาพ" อย่างต่อเนื่องครับ ไม่ใช่แค่ทำเพื่อให้ผ่านการตรวจประเมิน (Audit) เท่านั้น ถ้าเราใช้ Core Tools เป็น เราจะสามารถลดของเสีย ลดต้นทุน เพิ่มประสิทธิภาพ และที่สำคัญที่สุดคือ สร้างความพึงพอใจให้กับลูกค้าได้
เจาะลึก Core Tools แต่ละตัว (ภาคปฏิบัติ)
APQP (Advanced Product Quality Planning) และ Control Plan: วางแผนอย่างมืออาชีพ
APQP คืออะไร? ง่ายๆ เลยครับ มันคือกระบวนการวางแผนคุณภาพผลิตภัณฑ์ล่วงหน้า คิดตั้งแต่ก่อนจะเริ่มผลิตจริง เหมือนกับการวางแผนสร้างบ้าน ถ้าเราวางแผนดี บ้านก็จะออกมาสวยงาม แข็งแรง และตรงตามความต้องการ
ขั้นตอนของ APQP (5 เฟส)
APQP มี 5 เฟสหลักๆ ครับ:
- วางแผนและกำหนดโครงการ (Plan and Define Program)
- ออกแบบและพัฒนาผลิตภัณฑ์ (Product Design and Development)
- ออกแบบและพัฒนากระบวนการ (Process Design and Development)
- ตรวจสอบผลิตภัณฑ์และกระบวนการ (Product and Process Validation)
- ผลตอบรับ, การประเมิน และการปรับปรุง (Feedback Assessment and Corrective Action)
แต่ละเฟสก็จะมีกิจกรรมย่อยๆ ที่ต้องทำ ซึ่งรายละเอียดตรงนี้สำคัญมากๆ
การออกแบบกระบวนการผลิต
ในการออกแบบกระบวนการผลิต เราต้องคำนึงถึงปัจจัยต่างๆ มากมาย เช่น เครื่องจักร วัตถุดิบ วิธีการทำงาน บุคลากร ฯลฯ เพื่อให้ได้กระบวนการผลิตที่มีประสิทธิภาพ และสามารถผลิตสินค้าที่มีคุณภาพตามที่ต้องการได้
PPAP (Production Part Approval Process): อนุมัติชิ้นส่วนอย่างมั่นใจ
PPAP คือกระบวนการที่ Supplier ใช้ในการขออนุมัติชิ้นส่วนจากลูกค้า เพื่อให้มั่นใจว่าชิ้นส่วนนั้นๆ มีคุณภาพตามข้อกำหนด และสามารถนำไปใช้ในการผลิตได้
เอกสารที่จำเป็นสำหรับ PPAP
PPAP มีเอกสารหลายอย่างที่ต้องเตรียม เช่น PSW (Part Submission Warrant), Control Plan, FMEA, MSA, SPC, ฯลฯ แต่ละเอกสารก็มีความสำคัญแตกต่างกันไป
FMEA (Failure Mode and Effects Analysis): วิเคราะห์ความเสี่ยงเชิงรุก
FMEA คือเครื่องมือที่ใช้ในการวิเคราะห์ความเสี่ยง หรือ "จุดบอด" ที่อาจเกิดขึ้นในกระบวนการผลิต เพื่อหาทางป้องกันหรือลดผลกระทบที่อาจเกิดขึ้น
เทคนิคการทำ FMEA
การทำ FMEA ต้องทำเป็นทีม โดยระดมสมองกันเพื่อหาว่า "อะไรจะพังได้บ้าง?" (What can go wrong?) แล้วประเมินความรุนแรง (Severity), โอกาสที่จะเกิด (Occurrence), และความสามารถในการตรวจจับ (Detection) เพื่อจัดลำดับความสำคัญของความเสี่ยง
FMEA และ Control Plan
FMEA และ Control Plan มีความสัมพันธ์กันอย่างใกล้ชิด เพราะ Control Plan จะเป็นตัวกำหนดวิธีการควบคุมความเสี่ยงที่ระบุไว้ใน FMEA
SPC (Statistical Process Control): ควบคุมกระบวนการด้วยสถิติ
SPC คือการใช้สถิติในการควบคุมกระบวนการผลิต เพื่อให้มั่นใจว่ากระบวนการผลิตมีความเสถียร และสามารถผลิตสินค้าที่มีคุณภาพตามที่ต้องการได้
แผนภูมิควบคุม (Control Charts)
แผนภูมิควบคุม (Control Charts) เป็นเครื่องมือหลักของ SPC ใช้ในการติดตามแนวโน้มของกระบวนการผลิต และตรวจจับความผิดปกติที่อาจเกิดขึ้น
การตีความหมายแผนภูมิควบคุม
การอ่านและตีความแผนภูมิควบคุมเป็นทักษะที่สำคัญ เพราะจะช่วยให้เราเข้าใจว่ากระบวนการผลิตของเราเป็นอย่างไร และต้องปรับปรุงอะไรบ้าง
MSA (Measurement System Analysis): วิเคราะห์ระบบการวัดให้แม่นยำ
MSA คือการวิเคราะห์ระบบการวัด เพื่อให้มั่นใจว่าเครื่องมือวัดและวิธีการวัดของเรามีความแม่นยำและเชื่อถือได้ เพราะถ้าเครื่องมือวัดของเราไม่แม่นยำ เราก็ไม่สามารถวัดคุณภาพของสินค้าได้อย่างถูกต้อง
การทบทวน Core Tools เมื่อมีการเปลี่ยนแปลง
เมื่อมีการเปลี่ยนแปลงใดๆ เกิดขึ้น เช่น การเปลี่ยนแปลงการออกแบบผลิตภัณฑ์ การเปลี่ยนแปลงกระบวนการผลิต หรือการเปลี่ยนแปลงวัตถุดิบ เราจำเป็นต้องทบทวน Core Tools ที่เกี่ยวข้อง เพื่อให้มั่นใจว่า Core Tools เหล่านั้นยังคงมีความถูกต้องและเหมาะสม
ปัญหาที่พบบ่อยในการตรวจประเมิน (CB) และแนวทางแก้ไข
ปัญหาที่พบบ่อยในการตรวจประเมิน เช่น เอกสารไม่ครบถ้วน ข้อมูลไม่ถูกต้อง การไม่เข้าใจข้อกำหนด การไม่ปฏิบัติตามแผน ฯลฯ แนวทางแก้ไขคือ ต้องมีการเตรียมตัวที่ดี ทำความเข้าใจข้อกำหนดให้ชัดเจน ปฏิบัติตามแผนอย่างเคร่งครัด และมีการตรวจสอบภายในอย่างสม่ำเสมอ
สรุป: ก้าวสู่ความเป็นเลิศด้านคุณภาพด้วย Core Tools
Automotive Core Tools ไม่ใช่แค่ "ข้อบังคับ" ที่ต้องทำตาม แต่เป็น "เครื่องมือ" ที่จะช่วยให้องค์กรของคุณพัฒนาไปสู่ความเป็นเลิศด้านคุณภาพได้ ถ้าคุณเข้าใจและประยุกต์ใช้ Core Tools ได้อย่างถูกต้อง คุณก็จะสามารถลดต้นทุน เพิ่มประสิทธิภาพ และสร้างความพึงพอใจให้กับลูกค้าได้อย่างแน่นอน! อย่ารอช้าครับ เริ่มต้นเรียนรู้และลงมือทำตั้งแต่วันนี้เลย!
คำถามที่พบบ่อย (FAQs)
- Core Tools จำเป็นสำหรับทุกบริษัทในอุตสาหกรรมยานยนต์หรือไม่? จำเป็นอย่างยิ่งครับ โดยเฉพาะบริษัทที่เป็น Tier 1, Tier 2 Supplier ให้กับบริษัทผู้ผลิตรถยนต์ (OEM)
- ถ้าบริษัทไม่ได้ขอการรับรอง IATF 16949 ยังจำเป็นต้องใช้ Core Tools ไหม? ถึงแม้จะไม่ได้ขอการรับรอง แต่การใช้ Core Tools ก็ยังมีประโยชน์อย่างมากในการปรับปรุงคุณภาพและประสิทธิภาพของกระบวนการ
- การฝึกอบรม Core Tools จำเป็นสำหรับพนักงานทุกคนหรือไม่? ไม่จำเป็นต้องทุกคนครับ แต่ควรมีทีมงานหลักที่เข้าใจและสามารถนำ Core Tools ไปใช้ได้อย่างถูกต้อง
- มีแหล่งข้อมูลหรือเครื่องมือช่วยเหลือในการทำ Core Tools หรือไม่? มีครับ ทั้งหนังสือ คู่มือ ซอฟต์แวร์ และที่ปรึกษา ที่สามารถช่วยให้คุณทำ Core Tools ได้อย่างมีประสิทธิภาพ
- Core Tools มีการ Update หรือไม่ อย่างไร มีครับ มีการปรับปรุงอยู่เรื่อยๆ ควรติดตามข่าวสารจาก AIAG (Automotive Industry Action Group) ครับ
หลักสูตร เทคนิคการประยุกต์ใช้ Automotive Core Tools ภาคปฏิบัติ (APQP & Control, PPAP, FMEA, MSA, SPC
จากบทความที่แล้ว เราได้ทำความรู้จักกับ Automotive Core Tools ทั้ง 5 (APQP, PPAP, FMEA, MSA, SPC) และความสำคัญของเครื่องมือเหล่านี้ในการยกระดับคุณภาพในอุตสาหกรรมยานยนต์กันไปแล้ว คราวนี้เราจะมา "ต่อยอด" ความรู้เหล่านั้น ด้วยการลงลึกในรายละเอียด, เผยเคล็ดลับ, และยกตัวอย่างสถานการณ์จริง เพื่อให้คุณสามารถนำไปปรับใช้ในองค์กรได้อย่างมีประสิทธิภาพยิ่งขึ้น ไม่ใช่แค่ "ทำตาม" แต่ "เข้าใจ" อย่างแท้จริง!
APQP: มากกว่าแค่ Checklist
หลายคนมอง APQP เป็นเพียงรายการเอกสารที่ต้องทำให้ครบตาม Checklist แต่จริงๆ แล้ว หัวใจของ APQP คือ "การสื่อสาร" และ "การทำงานร่วมกัน" ระหว่างทีมงานต่างๆ (Cross-Functional Team) ตั้งแต่ฝ่ายออกแบบ, วิศวกรรม, การผลิต, คุณภาพ, ไปจนถึง Supplier
เคล็ดลับ: การประชุม APQP ที่มีประสิทธิภาพ
- กำหนดวาระการประชุม (Agenda) ที่ชัดเจน: ระบุหัวข้อที่จะหารือ, ผู้รับผิดชอบ, และเวลาที่ใช้ในแต่ละหัวข้อ ป้องกันการประชุมเยิ่นเย้อ เสียเวลาโดยใช่เหตุ
- ใช้ Visual Aids: ใช้แผนภูมิ, กราฟ, รูปภาพ, หรือแม้แต่ตัวอย่างชิ้นงานจริง เพื่อให้ทุกคนเข้าใจตรงกัน
- เปิดโอกาสให้ทุกคนแสดงความคิดเห็น: ส่งเสริมบรรยากาศที่ทุกคนกล้าแสดงความคิดเห็น และตั้งคำถาม แม้จะเป็นคำถามง่ายๆ ก็อาจนำไปสู่การค้นพบปัญหาที่สำคัญได้
- บันทึกการประชุม (Minutes) และติดตามผล (Follow-up): บันทึกประเด็นสำคัญ, ข้อตกลง, และผู้รับผิดชอบ พร้อมทั้งติดตามความคืบหน้าอย่างสม่ำเสมอ
ตัวอย่างสถานการณ์
ปัญหา: ฝ่ายออกแบบต้องการใช้วัสดุใหม่ที่มีน้ำหนักเบา แต่ฝ่ายผลิตกังวลว่าจะทำให้กระบวนการผลิตยากขึ้น
การแก้ไข: ทีมงาน APQP จัดประชุมเพื่อหารือ โดยเชิญผู้เชี่ยวชาญด้านวัสดุและผู้เชี่ยวชาญด้านกระบวนการผลิตมาร่วมให้ข้อมูล หลังจากวิเคราะห์ข้อมูลและทดลองผลิตตัวอย่าง ทีมงานก็สามารถหาข้อสรุปที่เป็นประโยชน์ต่อทุกฝ่ายได้
PPAP: สร้างความมั่นใจ ก่อนส่งมอบ
PPAP ไม่ใช่แค่การส่งเอกสารให้ลูกค้า แต่มันคือ "หลักประกัน" ว่าชิ้นส่วนของคุณมีคุณภาพตามข้อกำหนด และพร้อมสำหรับการผลิตจำนวนมาก (Mass Production)
เคล็ดลับ: การจัดการเอกสาร PPAP
- ใช้ระบบจัดเก็บเอกสารที่เป็นระเบียบ: ไม่ว่าจะเป็นระบบเอกสารแบบกระดาษหรือแบบอิเล็กทรอนิกส์ ต้องมีระบบที่สามารถค้นหาและเรียกดูเอกสารได้อย่างรวดเร็ว
- กำหนดผู้รับผิดชอบในการจัดทำและตรวจสอบเอกสาร: แต่ละเอกสารควรมีผู้รับผิดชอบที่ชัดเจน เพื่อป้องกันความสับสนและความผิดพลาด
- ตรวจสอบเอกสารอย่างละเอียด: ก่อนส่งเอกสารให้ลูกค้า ควรตรวจสอบให้แน่ใจว่าข้อมูลถูกต้องครบถ้วน และเป็นไปตามข้อกำหนด
- ทำความเข้าใจระดับการส่ง PPAP (Submission Levels): PPAP มีหลายระดับ (Level 1-5) แต่ละระดับก็มีข้อกำหนดที่แตกต่างกัน
ตัวอย่างสถานการณ์
ปัญหา: เอกสารไม่ครบถ้วน ข้อมูลไม่ถูกต้อง และไม่เป็นไปตามข้อกำหนด
การแก้ไข: Supplier ต้องรีบแก้ไขเอกสารให้ถูกต้อง และส่งให้ลูกค้าพิจารณาอีกครั้ง พร้อมทั้งทบทวนกระบวนการจัดทำเอกสาร PPAP ของตนเอง เพื่อป้องกันไม่ให้เกิดปัญหาซ้ำอีก
FMEA: มองไปข้างหน้า ป้องกันปัญหา
FMEA คือการ "คิดล่วงหน้า" ว่าจะมีอะไรผิดพลาดได้บ้าง (What could go wrong?) และจะป้องกันหรือลดผลกระทบได้อย่างไร มันคือการ "มองไปข้างหน้า" ไม่ใช่ "แก้ปัญหาเฉพาะหน้า"
เคล็ดลับ: การทำ FMEA ให้ได้ผล
- เริ่มตั้งแต่เนิ่นๆ: ควรทำ FMEA ตั้งแต่ขั้นตอนการออกแบบ ไม่ใช่รอจนใกล้จะผลิตจริง
- ใช้ข้อมูลจากหลายแหล่ง: รวบรวมข้อมูลจากประสบการณ์, บทเรียนจากอดีต (Lessons Learned), ข้อมูลจากลูกค้า, และข้อมูลจาก Supplier
- จัดลำดับความสำคัญของความเสี่ยง: ใช้ค่า RPN (Risk Priority Number) ในการจัดลำดับความสำคัญของความเสี่ยง และให้ความสำคัญกับความเสี่ยงที่มีค่า RPN สูงก่อน
- ทบทวน FMEA อย่างสม่ำเสมอ: FMEA ไม่ใช่เอกสารที่ทำครั้งเดียวจบ แต่ต้องมีการทบทวนและปรับปรุงอย่างสม่ำเสมอ เมื่อมีการเปลี่ยนแปลงใดๆ เกิดขึ้น
ตัวอย่างสถานการณ์
ปัญหา: พบว่ามีโอกาสที่ชิ้นส่วนจะเชื่อมไม่ติด ซึ่งอาจทำให้เกิดอันตรายต่อผู้ใช้งานได้
การแก้ไข: ทีมงาน FMEA กำหนดมาตรการควบคุม เช่น เพิ่มความถี่ในการตรวจสอบรอยเชื่อม ปรับปรุงวิธีการเชื่อม และฝึกอบรมพนักงานให้มีความชำนาญมากขึ้น
MSA: วัดให้แม่น ยำให้ถูก
ถ้าเครื่องมือวัดของเราไม่แม่นยำ เราก็ไม่สามารถมั่นใจในคุณภาพของสินค้าได้ MSA จึงเป็นเครื่องมือที่สำคัญในการ "วัดความสามารถของระบบการวัด" ของเรา
เคล็ดลับ: การทำ MSA ให้มีประสิทธิภาพ
- เลือกวิธีการ MSA ที่เหมาะสม: มีวิธีการ MSA หลายวิธี เช่น Gauge R&R, Attribute Agreement Analysis, Bias Study, Linearity Study เลือกใช้วิธีที่เหมาะสมกับลักษณะของข้อมูลและระบบการวัด
- เตรียมตัวอย่างและผู้ทำการวัดให้พร้อม: ตัวอย่างที่ใช้ในการทำ MSA ควรเป็นตัวแทนของชิ้นงานจริง และผู้ทำการวัดควรได้รับการฝึกอบรมมาอย่างดี
- วิเคราะห์ผล MSA อย่างละเอียด: ทำความเข้าใจผลลัพธ์ของ MSA และระบุสาเหตุของความแปรปรวนในระบบการวัด
- ปรับปรุงระบบการวัด (ถ้าจำเป็น): หากผล MSA ไม่เป็นที่น่าพอใจ ต้องดำเนินการปรับปรุงระบบการวัด เช่น ปรับปรุงเครื่องมือวัด เปลี่ยนวิธีการวัด หรือฝึกอบรมผู้ทำการวัดเพิ่มเติม
ตัวอย่างสถานการณ์
ปัญหา: เครื่องมือวัดแสดงค่าไม่ตรงกับความเป็นจริง ทำให้พนักงานคัดแยกชิ้นงานผิดพลาด
การแก้ไข: บริษัททำการ MSA เครื่องมือวัด พบว่าเครื่องมือวัดมีความแปรปรวนสูง จึงทำการปรับปรุงเครื่องมือวัด และฝึกอบรมพนักงานให้ใช้เครื่องมือวัดได้อย่างถูกต้อง
SPC: ควบคุมกระบวนการ ไม่ใช่แค่ตรวจจับ
SPC ไม่ใช่แค่การ "ตรวจจับ" ของเสีย แต่เป็นการ "ควบคุม" กระบวนการผลิต เพื่อให้สามารถผลิตสินค้าที่มีคุณภาพตามที่ต้องการได้อย่างสม่ำเสมอ
เคล็ดลับ: การใช้ SPC ให้เกิดประโยชน์สูงสุด
- เลือก Control Chart ที่เหมาะสม: มี Control Chart หลายประเภท เช่น Xbar-R Chart, Xbar-S Chart, p-Chart, np-Chart, c-Chart, u-Chart เลือกใช้ให้เหมาะสมกับลักษณะของข้อมูล
- กำหนด Control Limits ที่ถูกต้อง: Control Limits ไม่ใช่ Specification Limits Control Limits คำนวณจากข้อมูลของกระบวนการ ส่วน Specification Limits กำหนดโดยลูกค้า
- ตีความ Control Chart อย่างถูกต้อง: เรียนรู้วิธีการอ่านและตีความ Control Chart เพื่อระบุสัญญาณของความผิดปกติในกระบวนการ
- ดำเนินการแก้ไขเมื่อพบความผิดปกติ: เมื่อพบสัญญาณของความผิดปกติใน Control Chart ต้องรีบหาสาเหตุและดำเนินการแก้ไข เพื่อป้องกันไม่ให้เกิดของเสีย
ตัวอย่างสถานการณ์
ปัญหา: กระบวนการผลิตอาจเริ่มมีการเปลี่ยนแปลง ซึ่งอาจทำให้เกิดของเสียได้
การแก้ไข: พนักงานรีบแจ้งหัวหน้างาน หัวหน้างานตรวจสอบกระบวนการผลิต พบว่าเครื่องจักรเริ่มสึกหรอ จึงทำการซ่อมบำรุงเครื่องจักร ก่อนที่ปัญหาจะบานปลาย
สรุป: Core Tools เครื่องมือสู่ความสำเร็จ
Automotive Core Tools ไม่ใช่เรื่องยากอย่างที่คิด ถ้าคุณเข้าใจหลักการและนำไปปฏิบัติอย่างถูกต้อง เครื่องมือเหล่านี้จะช่วยให้คุณสามารถผลิตสินค้าที่มีคุณภาพ สร้างความพึงพอใจให้กับลูกค้า และเพิ่มขีดความสามารถในการแข่งขันขององค์กรได้อย่างแน่นอน!